Rails
The rails were fabricated on the sheet metal mold through hand layup process. Ten layers of carbon fiber were wet out with epoxy and laid in the tool. Adhesive spary was used on the first carbon fiber layer to avoid any potential resin scarcity in the corners. The mold was sealed with vacuum bag and pressure was applied through the vacuum at about 28 psi as it cured.
Steps
Steps were fabricated as a sandwich panel using a low-density foam as a core. The lay-up itself underwent a few different design iterations involving rod placement, ply counts, and overall layup procedure. This layup resulted in clean edges, easy processing, and well-defined anti-slip ridges. Problems occurred after a few uses of the mold as the polyurethane coating began to peel off the mold with the part, despite using several coats of mold release wax and liquid PVA film. Future solutions would be to build the mold of solid aluminum or use a tougher sealant instead of polyurethane.
Assembly
The steps and rails were bonded together with two-part epoxy. The wooden fixture was designed to hold the ladder components in right positions and provide support to the clamps.
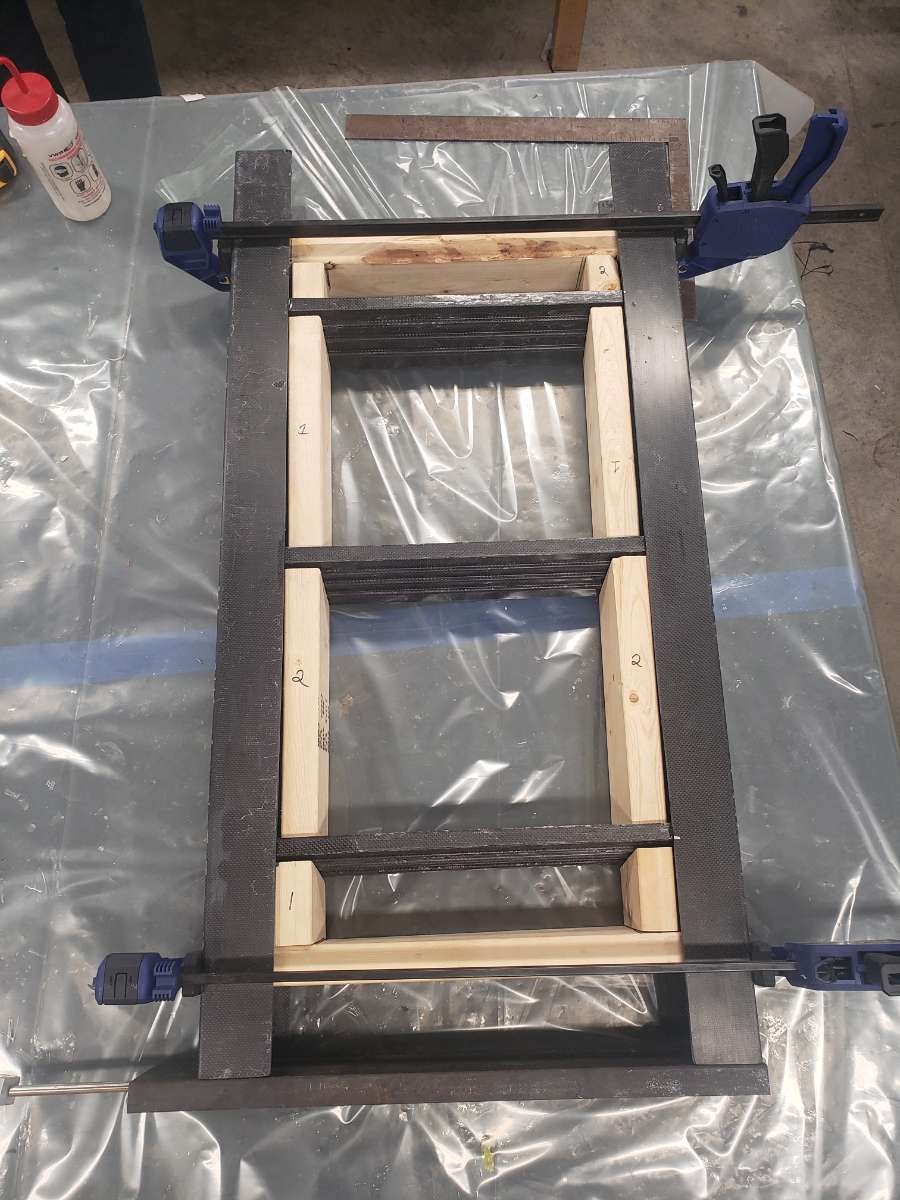